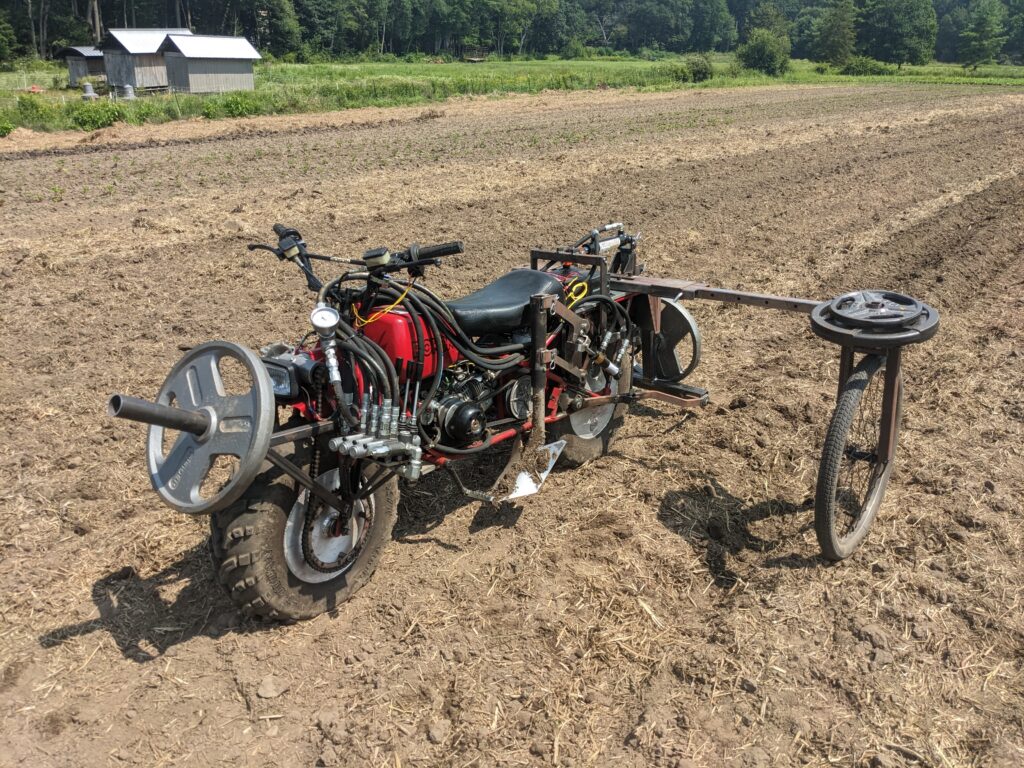
The Bullkey Tractor is the final product of my master’s degree in mechanical engineering. It’s the perfect combination of my love for engineering, science, metalworking and my childhood on the farm.
I inherited the project in 2021. Past graduate student Guillermo Diaz-Lankenau originated the idea and produced the original Bullkey prototype. While the original prototype excelled at proving the concept was scientifically viable, My job was to redesign this prototype and make it a product that would be successful in the open market.
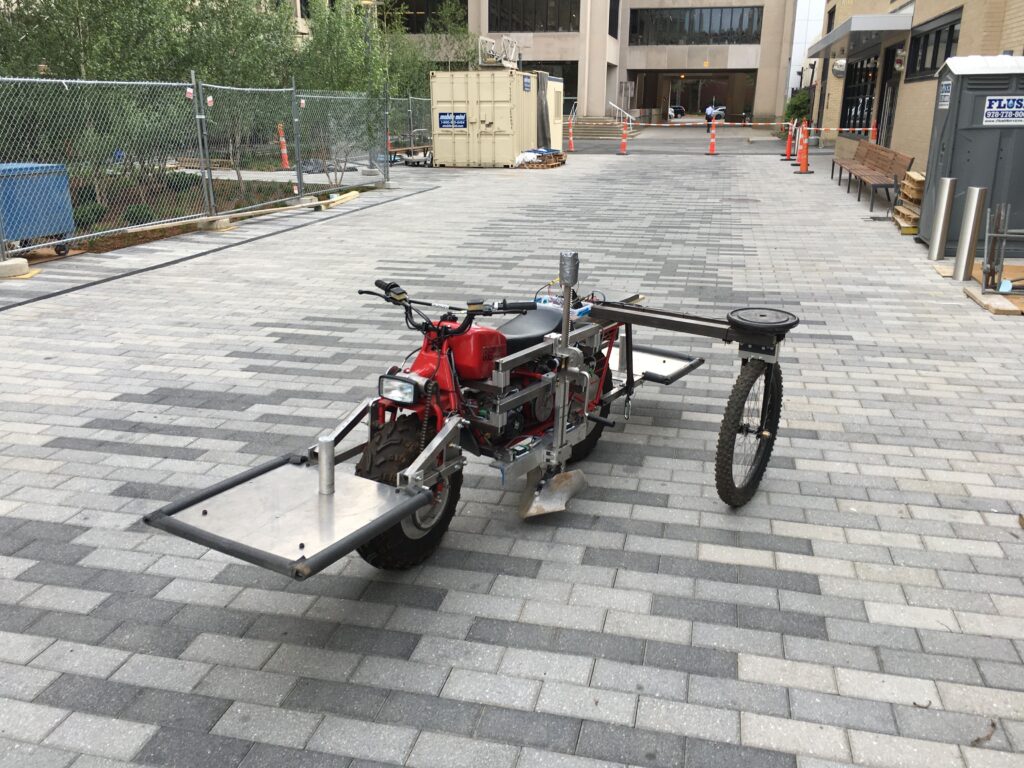
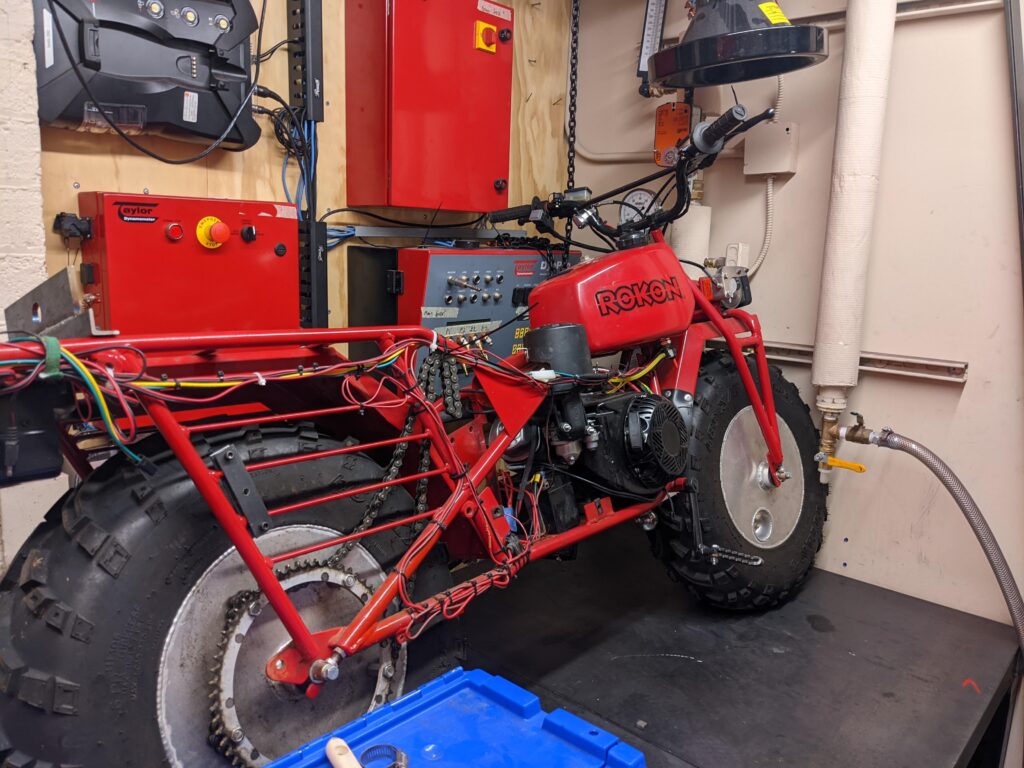
The original prototype had a number of ergonomic and aesthetic drawbacks which I needed to address. For one, the rack-and-pinion driven plow was a repetitive and uncomfortable motion for the operator. The size and location of the plow itself also prevented the rider from sitting on the motorcycle conventionally, forcing them to ride side-saddle. The ballast racks at the front and rear were called out for being tripping hazards, and the three-point hitch on the rear of the vehicle was very long, which would cause the vehicle to tip backwards if heavy loads were carried. The stabilizing “outrigger wheel” was a fixed length, limiting the number of crop-spacings that the Bullkey could tend.
The vehicle is based on a Rokon Scout: A two-wheel drive motorcycle manufactured in New Hampshire. The two-wheel drive layout and ultra-low-geared transmission creates the tremendous torque required for farming operations like plowing.
The Bullkey tractor is designed especially for low-income small-farmers. These farmers are responsible for over 70% of global food production, but perform many tasks by hand or with draft animals because modern farm equipment is much to expensive. They represent an enormous, untapped market in in need of low-cost, high performance machinery.
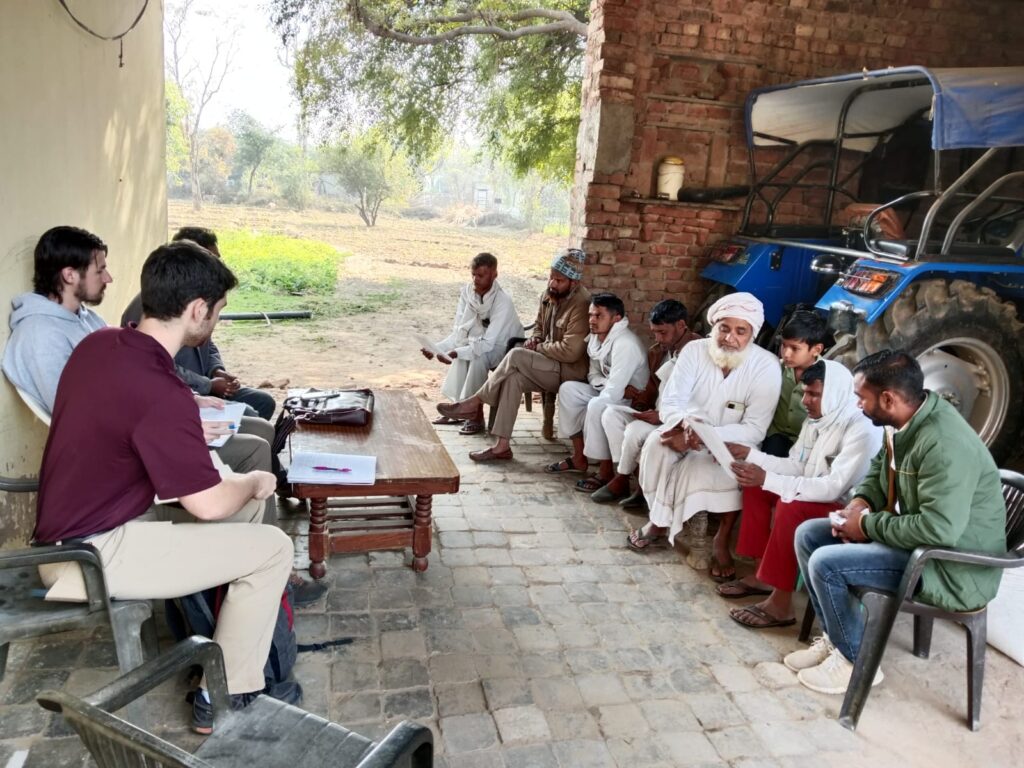
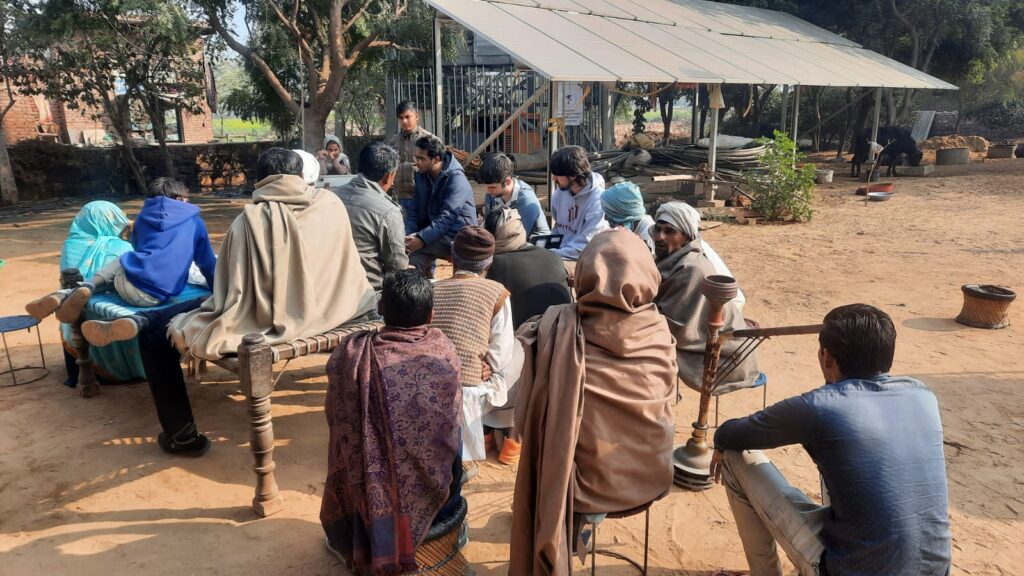
Over the course of the project, I visited India three times. India has over 125 million small farms – more than any other country by long shot. In total, I spoke with over 300 farmers about there practices and what they would look for in a piece of a new farm equipment designed just for them. These farmers gave us some new insights to consider as well: The Bullkey tractor would need a power-take-off (PTO) in order to compete with modern farm machinery. Similarly, due to its narrow and nimble format, farmers felt it would be especially valuable to driving between rows of tall crops like corn or cotton for pesticide application; this task is normally completed by laborers with backpack-style sprayers, which is very hazardous for their health.
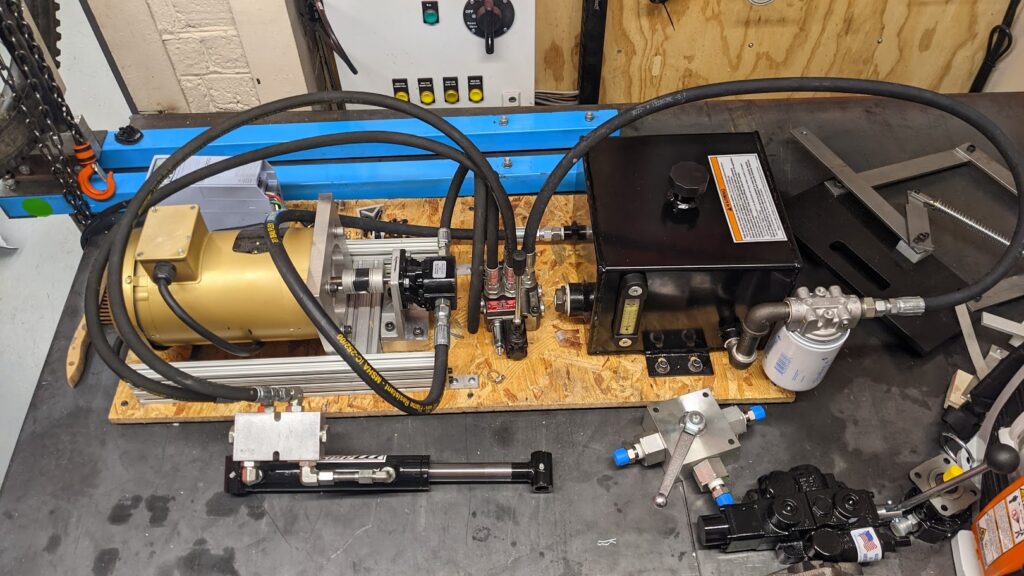
While in order to redesign the plow and 3 point hitch, and to implement a PTO, I decided to implement a complete hydraulic circuit on the Bullkey. Hydraulic components are cheap, ubiquitous, and easy to maintain or replace. I began with a bench-test where a hydraulic pump is driven by an electric motor. The circuit, consisting of a filter, reservoir, pump, control valve and hydraulic cylinder, was the earliest stage of this development.
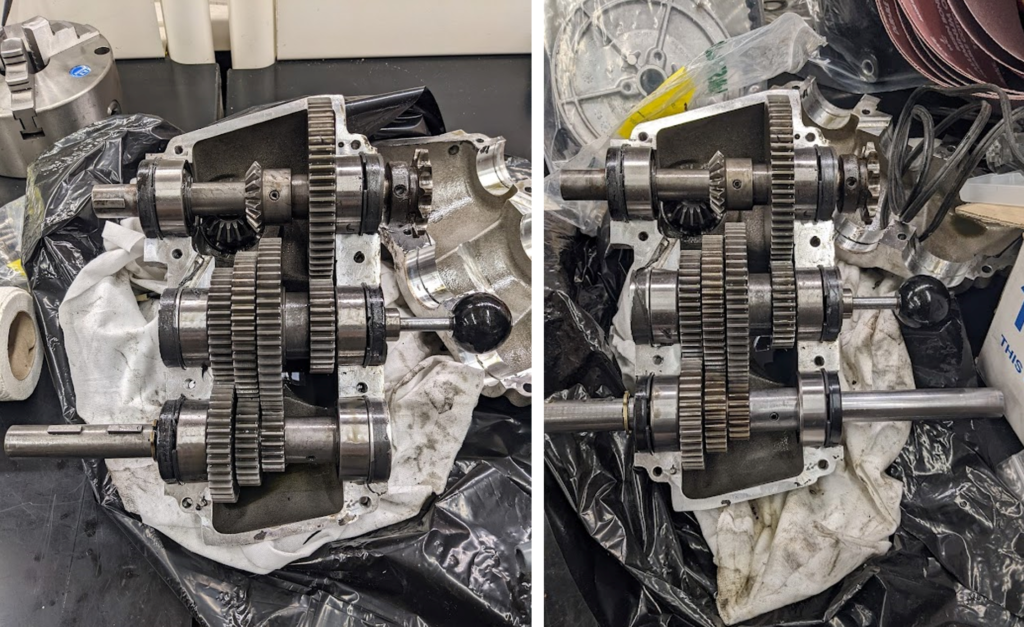
In order to power the hydraulic pump, I needed to modify the transmission of the Rokon to support an additional power output. after disassembling the transmission, I was able to re-machine the lower “input shaft” where power is delivered to the transmission from the engine. By extending this shaft an additional 5 inches and adding an additional bearing and oil seal, I created a by-way for engine power to pass through the transmission and power another system: The hydraulic pump.
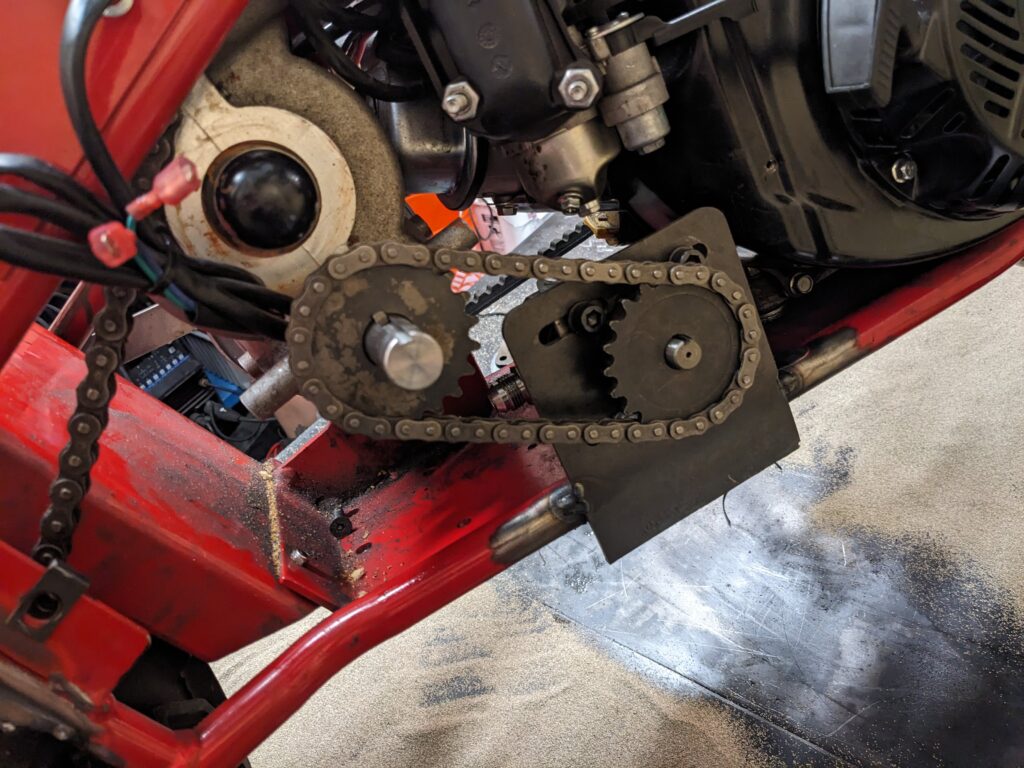
With the modified transmission re-installed, I worked with a student team from the MIT 2.76 “Global Engineering” class to install the hydraulic pump on the vehicle. We relocated the battery and used the space it left behind to install the pump by bolting it to a small weldment added to the frame. The oil filter was attacked underneath the seat, and I designed a custom, low-profile oil reservoir to mount behind the rider. To mount the valve, I first laser-cut an acrylic model and attached it to the frame with hot glue. This is an easy and effective way to test to the ergonomics, as the model can be removed with a heat gun instead of cutting off welds with a grinder.
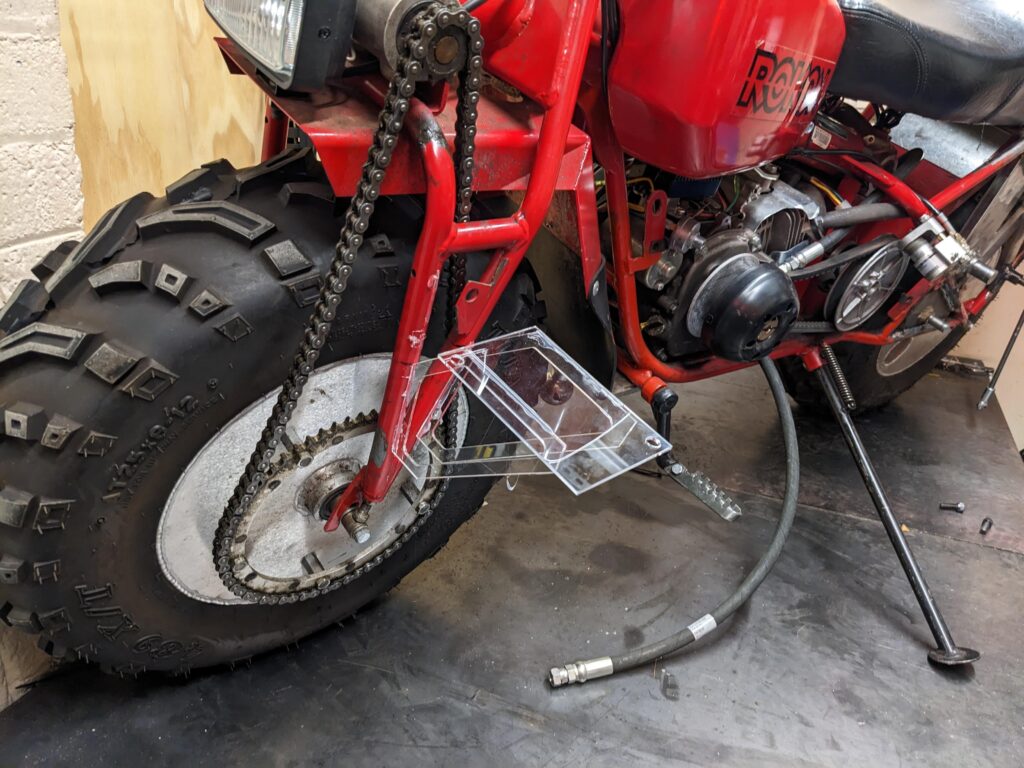
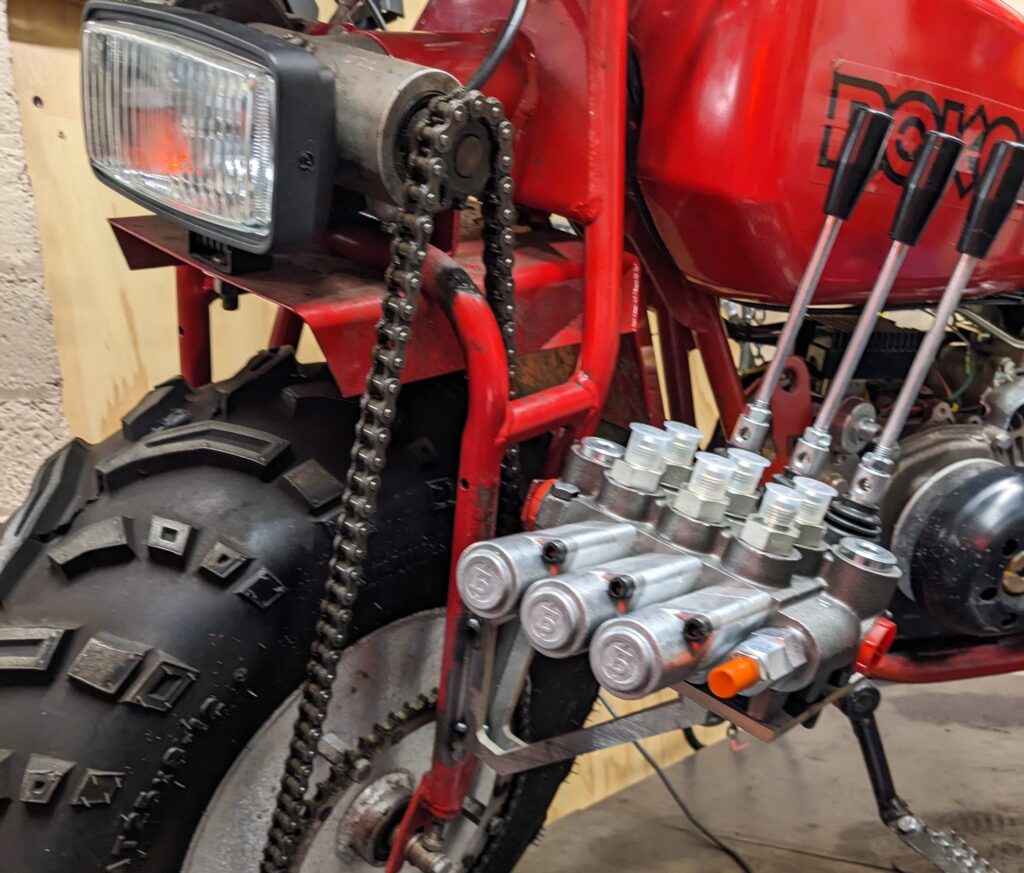
After a lengthy design process involving analytical solutions to mechanical linkages, an iterative optimizing program coded in MATLAB, and failure simulations in SolidWorks, a new plow and 3-pt hitch were designed and manufactured. In order to install them, the frame of the Rokon needed to be heavily modified, requiring yet more analysis, design and manufacturing.
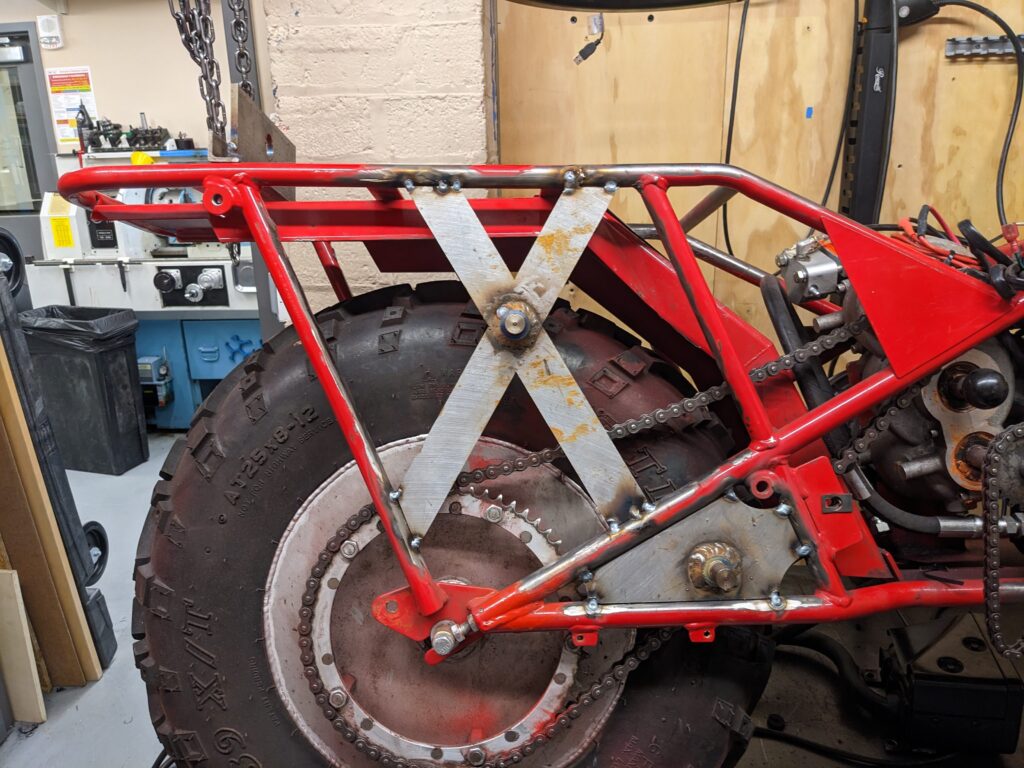
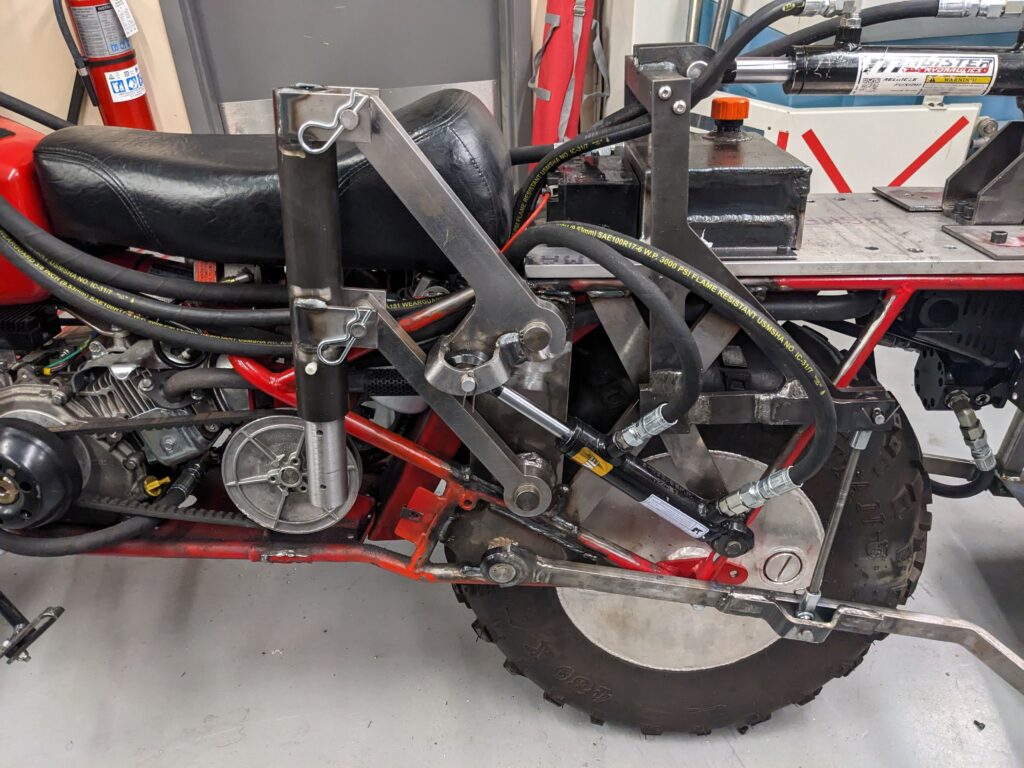
The frame modifications were made from water-jet-cut mild steel and machined tool-steel posts for pivots, welded into the mild steel.
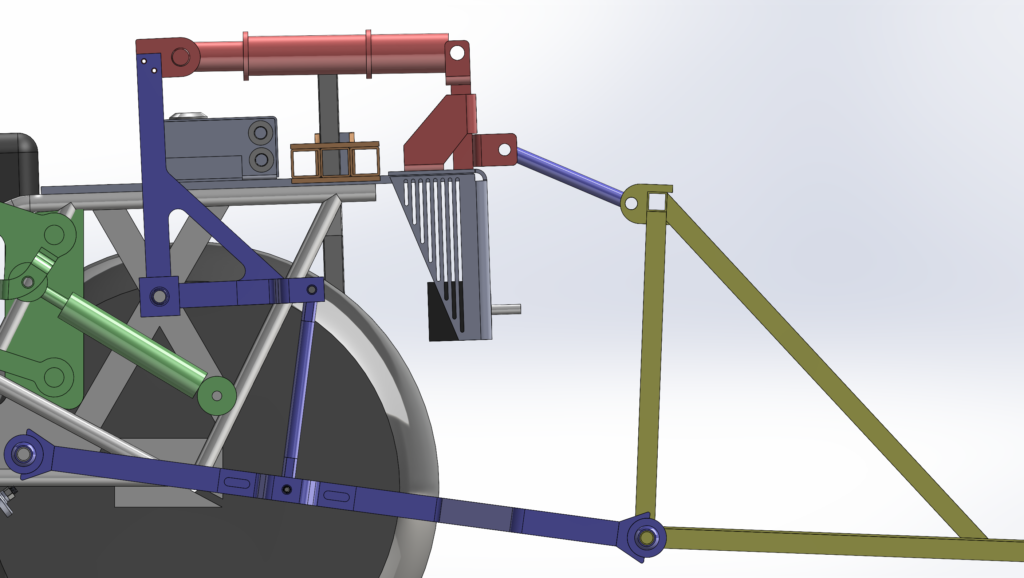
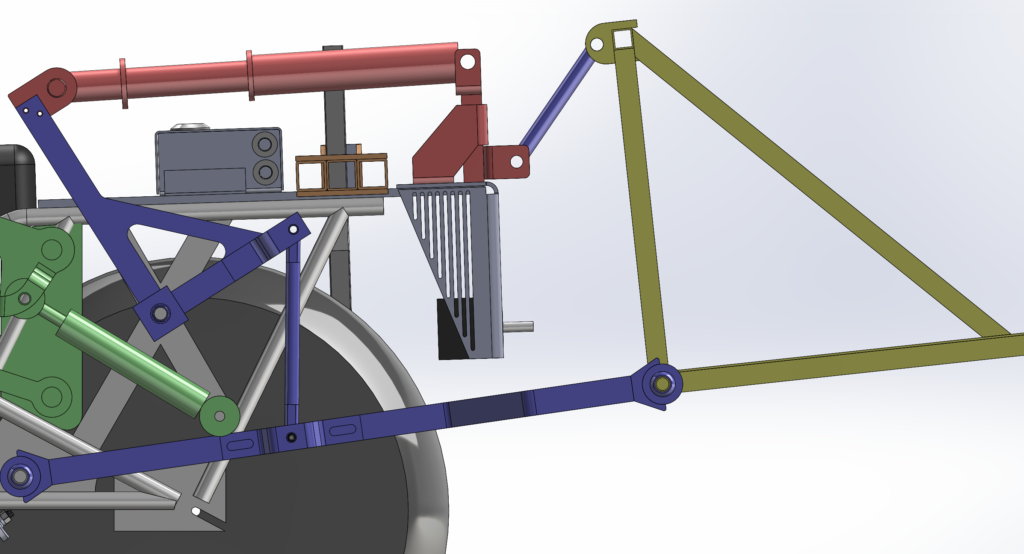
The linkage for the 3-point hitch is a compact 6-bar that uses a single, center-mounted hydraulic cylinder to raise the load.
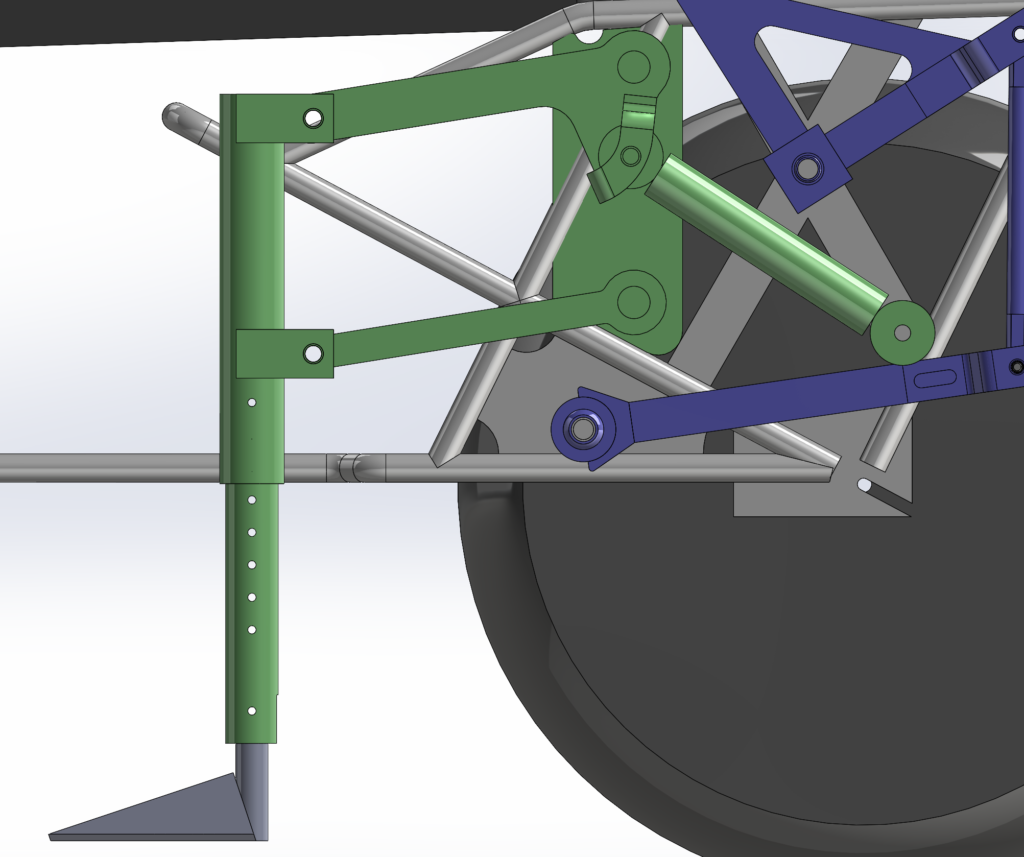
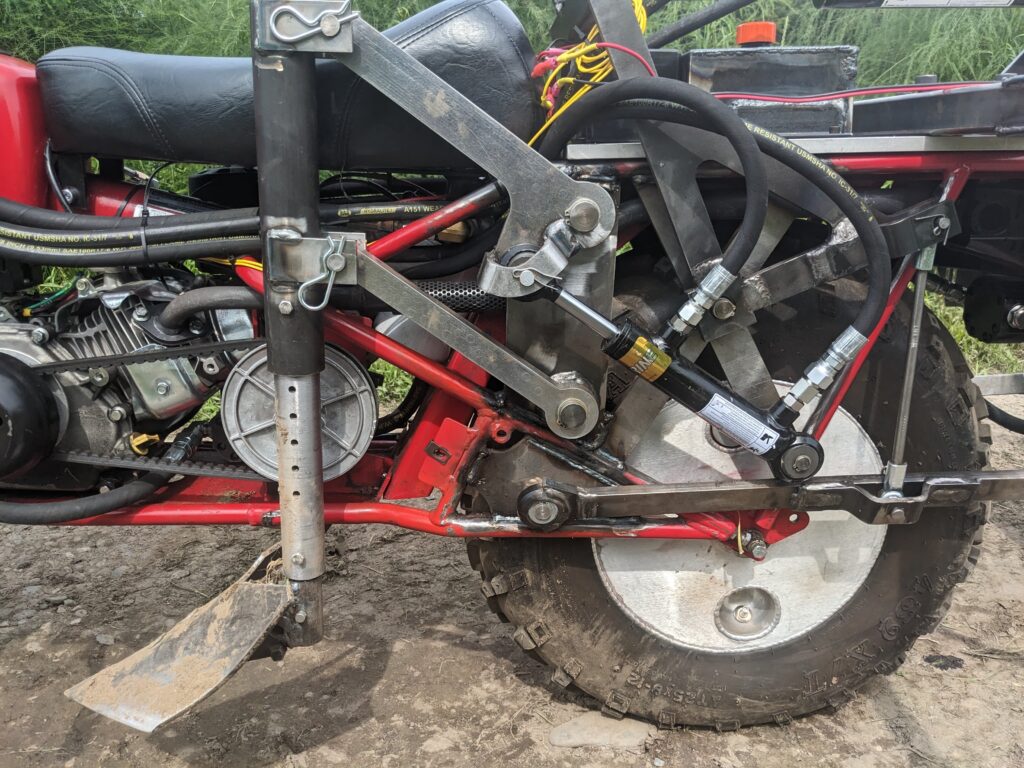
The plow is a simple 5 bar linkage driven by a small hydraulic cylinder. The more compact profile does not interfere with sitting on the bike conventionally
More coming soon! Back to work now…